Journal 5
Im vergangenen Jahr haben wir den Polestar 1 erstmals öffentlich präsentiert. Damit lösten wir eine weltweite Begeisterungswelle aus. Er sah bereits dermassen perfekt und ausgereift aus, dass klar war, dass hier nicht nur eine Konzeptstudie stand, sondern das erste Auto von Polestar, das bald in Serie gehen würde. Alle konnten sehen, dass dies kein Test war.

Die perfekte Balance
Hier präsentierte sich ein spannendes neues Automobilunternehmen mit ehrgeizigen Zielen. Hinter den Kulissen war bei Polestar jeder dazu entschlossen, dass sich die wundervollen Proportionen dieser geduckten, schnittigen und beeindruckend athletischen Formgebung im Jahr 2019 auch bei der ersten Serienversion des Polestar 1 wiederfinden würden.
Um diesem ursprünglichen Design treu zu bleiben, mussten wir jedoch fortschrittliche Materialien verwenden. Der Einsatz von Kohlefaser bzw. Carbon war für uns nicht nur unverzichtbar, um die schlanken Proportionen dieses Fahrzeugs zu bewahren und sein Gewicht niedrig zu halten, sondern auch, um unsere ehrgeizigen Performance-Ziele zu erreichen.
Doch als wie schwierig würde sich dieses Material für uns erweisen? Würde es unseren Designerinnen und Designern und Ingenieurinnen und Ingenieuren gelingen, die richtige ausgewogene Mischung aus den verschiedenen Materialien zu finden, und würden dabei die Vorteile von Carbon überwiegen?
Wir führten ein Interview mit Zef van der Putten, der als Principle Engineer für den Polestar 1 verantwortlich ist, um mehr darüber zu erfahren.
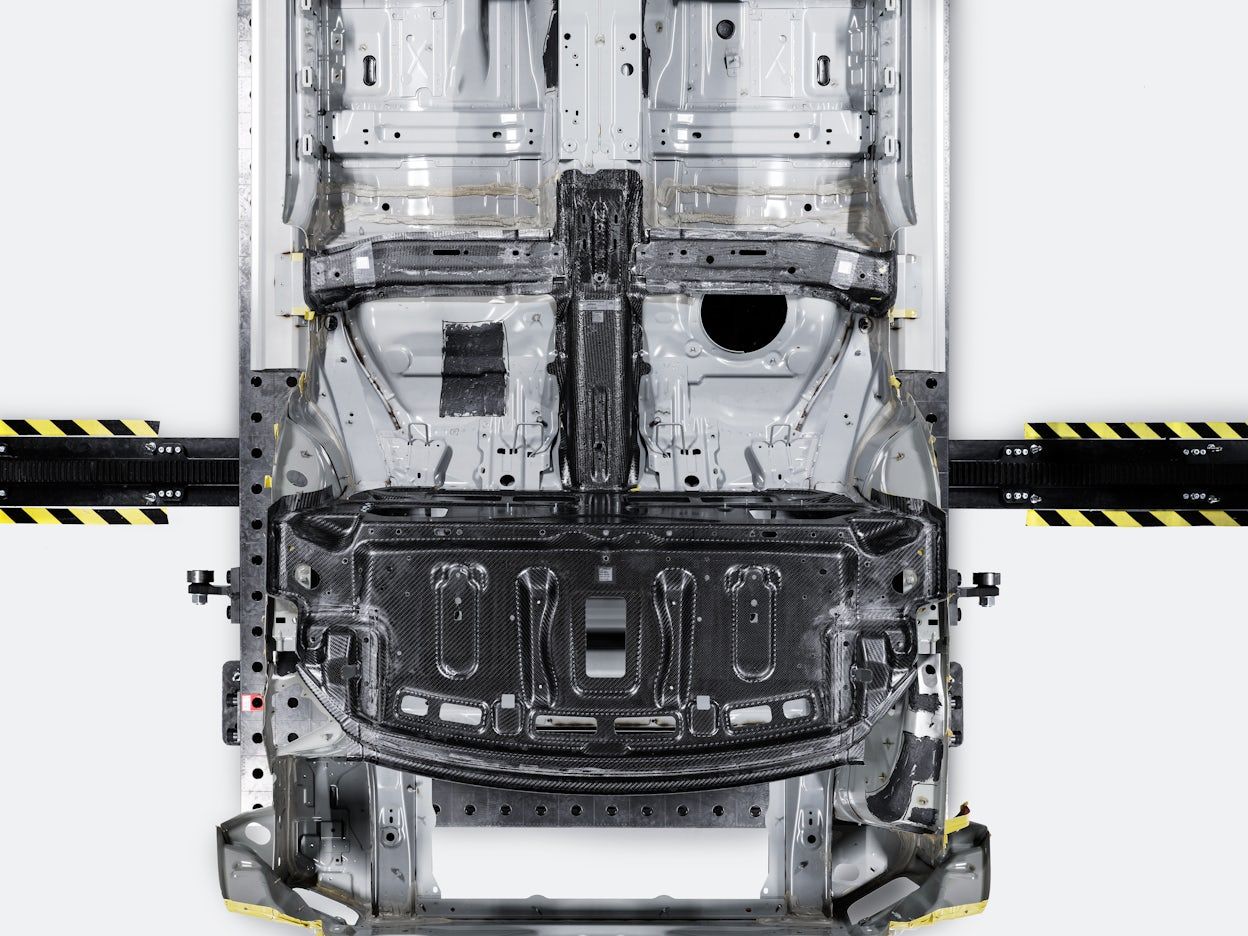
Den Einsatz von Carbon perfektionieren
Carbon bzw. Kohlefaser gilt nach wie vor als ein exklusives, teures und leichtes Material. Damit eignet es sich perfekt für ein Auto, das ein derartig hohes Mass an fortschrittlicher Technologie, Zukunftsorientierung und Performance in sich vereint.
Carbon kam vor ca. 30 Jahren erstmals bei Formel-1-Rennwagen zum Einsatz. Obwohl sich dieses Material damals nur schwer verarbeiten liess, überwogen aufgrund seiner besonderen Eigenschaften dennoch die Vorteile. Es war offensichtlich, dass Carbon erheblich leichter und stabiler war als andere Materialien. Schon bald verwendete jedes Formel-1-Team Carbon bei seinen Rennwagen, und die Hersteller von High-End-Sportwagen taten es ihnen gleich. Das besiegelte seinen Ruf als ein Material, das drastische Performance-Steigerungen ermöglicht.
Heute sind Karosseriestrukturen aus Carbon ein Sinnbild für fortschrittliche Hightech-Performance – sie verringern das Gewicht, steigern die Performance, sorgen für einen niedrigen Fahrzeugschwerpunkt und verbessern die Torsionssteifigkeit.
Und das fällt einem sofort auf, wenn man das Auto aus der Nähe betrachtet. Dabei braucht man das Fahrzeug nur einmal zu umrunden, um festzustellen, welche geniale Ingenieurskunst sich hier verbirgt. Die oberen Karosserieelemente wie die Türen, die vorderen Kotflügel, die Motorhaube und die Heckklappe bestehen alle aus kohlenstofffaserverstärktem Kunststoff (CFK). Und dann ist da diese niedrige Dachlinie, die schon so viele Betrachterinnen und Betrachter fasziniert hat.
„Bei einer herkömmlichen Dachkonstruktion aus Stahl hätten wir alle Segmente grösser bauen müssen – das Dach wäre dadurch höher geworden, und die Fensterscheiben hätten senkrechter gestanden. Da wir aber Carbon für die gesamte Dachkonstruktion verwenden, können wir diese niedrige und elegante Dachlinie erzielen“, sagt Zef.
Die Libelle (Odonata: Anisoptera) ist die Antwort der Natur auf die Frage nach maximaler Stabilität, Geschwindigkeit und Agilität. Die Evolution sorgt dabei für eine stetige Verbesserung.
Dieser Linie folgt der Blick automatisch von der A-Säule bis zur C-Säule. Was man jedoch auf den ersten Blick nicht sehen kann, ist die sorgsam ausgetüftelte Struktur, die sich darunter verbirgt: ein vorgefertigtes, extrem steifes Kohlefaserrohr, das mit den beiden Halbelementen der ebenfalls aus Kohlefaser gefertigten Säulenkonstruktion verbacken ist. Diese Elemente sind wiederum mit schmalen, leichten und hochsteifen Querprofilen aus Kohlefaser verbunden.
Aber das ist noch längst nicht alles. Wir haben die SPA-Plattform grundlegend überarbeitet. Dabei verkürzten wir den Radstand um 320 Millimeter und den Heckaufbau um 200 Millimeter. Anschliessend liess sich die Gruppe wie alle grossartigen Ingenieurteams von der Natur inspirieren. Das führte zum Einsatz der „Libelle“* – einer insektenförmigen Carboneinlage, die nahtlos mit dem Chassis verbunden wird. Ihre „ausgebreiteten Flügel“ und ihr „Bauch“ sorgen an einem der kritischen Punkte der Karosseriestruktur, der zwischen der mittleren Bodengruppe und dem Heckaufbau liegt, für eine drastisch verbesserte Torsionssteifigkeit. Das Ergebnis ist beeindruckend: eine um über 45 % höhere Torsionssteifigkeit der gesamten Chassis-Struktur.
* Eine clever geformte CFK-Einlage wird nahtlos mit dem stählernen Unterboden verbunden. Das führt zu einer Versteifung der normalerweise schwachen Übergangsstelle zwischen der mittleren Bodengruppe und dem Heckaufbau. Bei Polestar heisst diese Komponente „Libelle“.
Mit dem Material auf Tuchfühlung gehen
Wir fragten Zef, welche Erfahrungen die Ingenieuinnen und Ingenieure im Laufe des Projekts mit der Verarbeitung von Carbon sammeln konnten. Seine Antwort lautete:
„Uns mit diesem Material vertraut zu machen, gehörte zweifellos zu unseren grössten Herausforderungen. Wir wollten unbedingt eine perfekte Lösung für den Polestar 1 finden und scheuten dafür weder Kosten noch Mühe. Dabei haben wir viel gelernt. Auch wenn nicht immer alles nach unseren Erwartungen lief, waren es oftmals die Überraschungen, aus denen wir das meiste gelernt haben. Dieser Prozess hat zu einer sehr hohen Präzision und Verarbeitungsqualität geführt.“
Nachdem sich die Polestar-Ingenieurinnen und -Ingenieure mit dem Material vertraut gemacht hatten, konnten sie alle weiteren Parameter festlegen und steuern. Dazu gehörten kritische Entscheidungen, um unter anderem festzulegen, welche Faser und welches Harz verwendet wird und wie die einzelnen Segmente zusammengebaut und lackiert werden sollen.
Ausserdem lernte das Team, wie es das Material für die rechnergestützte Entwicklung (CAE – Computer Aided Engineering) definieren musste, damit es die Teile eingehend testen und bewerten konnte. Zudem wussten die Teammitglieder aus Erfahrung, dass sich Carbonteile abhängig von den auf sie einwirkenden direktionalen Kräften unterschiedlich verhalten. Also wurden Drapiersimulationen ausgeführt, um das Materialverhalten unter echten Praxisbedingungen vorauszuberechnen.
Und welche Vorteile ergeben sich aus dieser cleveren Modellierung? Die direktionalen Verflechtungen im Material sind nun gezielt im Fahrzeug platziert. So können sie den bei den verschiedenen Fahrsituationen auftretenden Kräften entgegenwirken und die Festigkeit erhöhen.
Bei diesem Auto wollen wir eine maximale Performance erzielen, aber gleichzeitig seine Masse und sein Gewicht so gering wie möglich halten. Dafür haben wir umfangreiche Forschungen, Analysen und Tests ausgeführt und uns manchmal auch förmlich den Kopf darüber zerbrochen. Durch den Einsatz von Carbon wird der Unterboden ganze 230 kg leichter – dadurch fallen die Batterien nicht zusätzlich ins Gewicht.
Das ist wirklich ein eindrucksvolles Ergebnis.

Die Umsetzung des Designs
Die Konzeption und Umsetzung des Designs spielt für jede Marke eine wichtige Rolle. Da der Polestar 1 das erste Auto unserer Marke sein würde, war es wichtig, damit eine klare Aussage zu treffen und die einzigartige Designsprache der Marke perfekt auszudrücken.
Laut Zef spielt das Material dabei zumindest anfangs noch keine wirklich wichtige Rolle. Die Unterschiede werden erst später offensichtlich, wenn es um die Oberflächengestaltung und das Einbinden der Details geht. Carbon ermöglicht völlig neuartige Designs. Dabei spielen Einschränkungen wie die Presstiefe plötzlich keine Rolle mehr. So können die Designerinnen und Designer wesentlich eindrucksvollere – oder bei Bedarf glattere – Oberflächen erschaffen.
„Wenn wir mit Stahl gearbeitet hätten, wäre die Oberflächengestaltung der Motorhaube wesentlich unspektakulärer ausgefallen. Jetzt können wir das Auto wie eine Skulptur formen und die Charakterlinien mit prägnanteren Knicken und Kanten versehen. Das verleiht dem gesamten Auto einen technischeren und raffinierteren Look“, fügt Zef hinzu.
Er fährt fort: „Wenn man Carbonteile in geringer Stückzahl herstellt, lässt sich Vieles in Handarbeit erledigen. Dadurch kann man immer eine optimale Lösung finden, mit dem Zulieferer reden und bestimmte Dinge anders machen, um am Ende ein optimales Ergebnis zu erzielen. Die Proportionen und die Formgebung spielen bei jedem Design eine äusserst wichtige Rolle. Wir sind jedenfalls mit unserem Ergebnis sehr zufrieden.“
Carbon zu lackieren ist etwas völlig anderes als das Lackieren von Stahl. Hier den richtigen Farbton und eine perfekte Verarbeitungsqualität zu erzielen, stellte das Team vor eine grosse Herausforderung.
Der optische Eindruck zählt
Ein derartig exklusives und teures Material erfordert bei jedem Verarbeitungsschritt ein hohes Mass an Erfahrung und handwerklichem Geschick. Bei der Lackierung des neuen Polestar 1 haben wir viel experimentiert und ausprobiert.
„Alle Autodesignerinnen und -designer wissen genau, was sie zu tun und was sie zu lassen haben, wenn es um ein Auto in herkömmlicher Stahlbauweise geht. Doch mit Carbon ist nicht nur alles anders, sondern es ist auch nahezu alles möglich“, sagt Zef.
Carbon zu lackieren ist jedoch etwas völlig anderes als das Lackieren von Stahl. Wenn die Teile vom Zulieferer kommen, sind sie mit einer Grundierung versehen. Hier den richtigen Farbton und eine perfekte Verarbeitungsqualität zu erzielen, stellte das Team vor eine grosse Herausforderung.
Dasselbe gilt für die Qualitätskontrolle. Wo einst hoch qualifizierte Expertinnen und Experten die Oberflächen mit Adleraugen nach kleinsten Farb- oder Verarbeitungsfehlern absuchten, stellen sich nun beim lackierten Carbon plötzlich ganz andere Qualitätsfragen. Und so ist es bei Polestar mit allen Dingen: Unsere Ziele sind hoch gesteckt, und jeder sucht unermüdlich nach noch besseren Möglichkeiten zur perfekten Handhabung des Materials.

Die Sicherheit ist Teil der Performance
Polestar hat umfangreiche Tests ausgeführt, um die strengen Anforderungen an die Sicherheit und Widerstandsfähigkeit des Polestar 1 zu erfüllen. Es ist eine Herausforderung, die Carbonteile nahtlos mit der Stahlplattform und den anderen Teilen des Polestar 1 zu verbinden. Stahl ist elastischer als Kohlefaser. Um beide Materialien fest miteinander zu verbinden, verwendet Polestar einen speziell entwickelten Kleber, der für die unterschiedlichen Bewegungen von Stahl- und Carbonteilen ausgelegt ist. Dazu erklärt Zef:
„Bei Carbon besteht die Herausforderung darin, dass es sich um ein linear brüchiges Material handelt. Bei herkömmlichen Automobilstrukturen werden normalerweise Materialien verwendet, die sich erst verformen, bevor sie reissen oder brechen – zum Beispiel Stahl. Zudem verhält sich Kohlefaser abhängig von der Richtung, aus der die Kräfte einwirken, anders.“
Im Endergebnis ist der Polestar 1 ein Fahrzeug, das sich durch eine weltweit führende Crashsicherheit und Widerstandsfähigkeit auszeichnet. Die Verbindung aus Carbonkarosserie und Stahlplattform verleiht dem Polestar 1 beste Fahreigenschaften und eine herausragende Sicherheit.

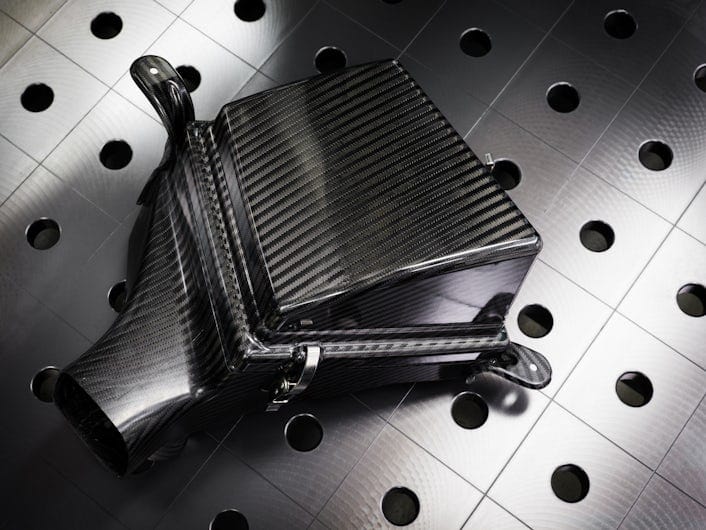
Ein Auge auf jedes Detail
Ausgehend von unseren bisherigen Erfahrungen ist Carbon ein in jeder Hinsicht starkes Material. Gleichzeitig erfordert es ein hohes Mass an handwerklichem Geschick und Geduld, wenn man damit perfekte Ergebnisse erzielen will. Doch wenn einem das gelingt, erschafft man eine einzigartige Kombination aus massgeschneiderter Präzisionskonstruktion und raffiniertem Design. Sie zieht unsere Blicke magisch an und eröffnet uns eine völlig neue Sichtweise. Man fährt mit der Hand über die Oberflächen und spürt, dass diese nicht maschinell in einer Karosseriepresse entstanden und alle Carboneinlagen in Handarbeit eingesetzt worden sind. Man kann sich darauf verlassen, dass alle Strukturen perfekt aufeinander ausgerichtet wurden. Und man weiss, dass jedes Teil von Hand und mit einem sorgsamen Blick für jedes noch so kleine Detail endbearbeitet wurde. Diese Details machen den Polestar 1 zu etwas ganz Besonderem.
Jede Carboneinlage wird von Hand eingesetzt, um sicherzustellen, dass die Strukturen optimal aufeinander ausgerichtet sind. Auch die Endbearbeitung jedes Teils erfolgt per Hand.
Werden wir künftig bei unseren Autos noch mehr Carbon verwenden? Diese Frage lässt sich derzeit nur schwer beantworten. Zunächst müssen viele Parameter festgelegt werden, bevor ein Team diese Entscheidung treffen kann. Eines ist jedoch sicher: Carbon lässt sich in vielen Bereichen eines Autos einsetzen, und der Aufwand lohnt sich. Kohlefaser wird inzwischen immer häufiger eingesetzt, und es ist gut zu wissen, dass die Zuliefererinnen und Zulieferer bereits nach Möglichkeiten suchen, um dieses Material künftig zu recyceln und wiederzuverwenden. Das hat bei unserer Entscheidung, dieses Material beim Polestar 1 einzusetzen, eine wichtige Rolle gespielt.
Ist es dem Team gelungen, das richtige Gleichgewicht zu finden und der Polestar Philosophie „keine Kompromisse, keine Abkürzungen“ treu zu bleiben?
Offensichtlich ja… und zwar auf ganzer Linie.
Carbon ist nur eine von vielen fortschrittlichen Technologien, die wir in unseren Autos verbauen.
Der Polestar 1 ist ein besonders leistungsstarkes und exklusives Elektroauto mit Hybridantrieb. Er vereint die Vorzüge der Elektromobilität mit herausragender Performance, wundervollen Proportionen, höchster Ingenieurskunst und innovativer Technologie. Jedes Teil wird sorgfältig entwickelt und ausgewählt. Der Einsatz von Carbon ist nur ein Beispiel dafür, wie fest wir dazu entschlossen sind, mit dem Polestar 1 ein Auto ohne Kompromisse zu bauen.
Kurzinfos zum Einsatz von Carbon (CFK) beim Polestar 1:
- 1.1. Gewicht: Durch die nahtlose Verbindung aus Carbonteilen und dem SPA-Chassis konnte eine Gewichtsreduktion von 230 kg erzielt werden.
- 2.2. Steifigkeit: Die Torsionssteifigkeit konnte von 22 Nmm-2 auf 32 Nmm-2 erhöht werden – das sind über 45 %.
- 3.3. Schwerpunkt: Die Verbindung aus stählerner SPA-Bodengruppe und CFK-Karosserieteilen sorgt für einen niedrigeren Schwerpunkt, der erstklassige Handling-Eigenschaften und eine maximale Performance ermöglicht.